本田公司自20世纪80年代末开始进行燃料电池的基础研究。如今,为了满足包括乘用车、商用车以及固定电源在内的多种应用需求,进一步提升燃料电池的耐久性并降低成本已变得尤为迫切。在此背景下,本田与通用汽车联合开发出一种全新的燃料电池堆结构,其耐久性提升至原来的两倍以上,而成本降低至原来的三分之一,同时保持了出色的输出性能。该燃料电池堆的一体化电极组合(Unitized Electrode Assembly,UEA)由膜电极(MEA)和其外部的树脂框架结构组成,膜电极负责电力的产生。
传统的UEA中,电极催化剂和质子传导膜使用了大量的铂(Pt)和离子体(ionomer),这些材料虽然提高了耐久性,但也大幅增加了成本。此外,受限于发电单元的设计,外部树脂结构采用注塑成型工艺,需要至少250微米的厚度来确保成型性,因此难以通过减薄单电池来提高功率密度。
01 UEA开发目标
此前燃料电池堆中UEA的结构如图1所示。整个发电单元由两个UEA夹在三片不锈钢(SUS)双极板之间组成,数百个这样的发电单元堆叠在一起形成一个燃料电池堆。UEA由膜电极组件(MEA)和外部树脂结构构成。
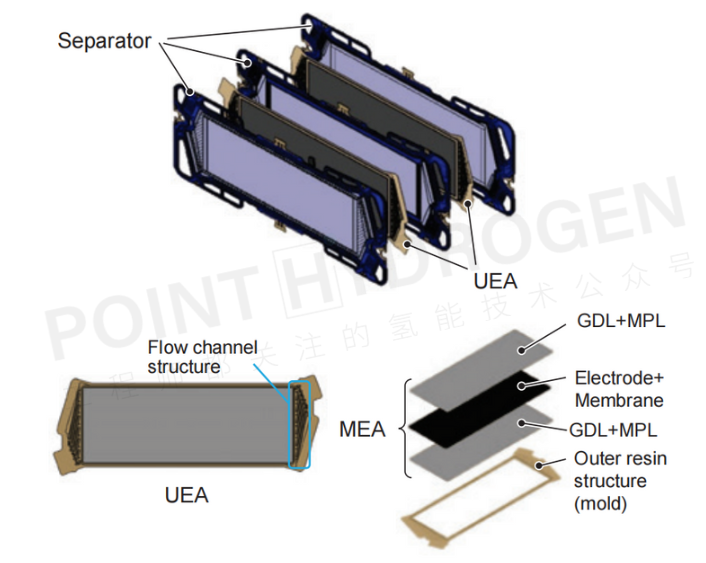
图2显示了以往UEA材料成本的细分,阴极催化剂和电解质膜占据了成本的主要部分。电极催化剂中的铂(Pt)和电解质膜的主要成分离子体(ionomer)都是昂贵且难以大规模生产的,因此减少这些材料的使用是降低UEA成本的有效途径。同时,气体扩散层(GDL)在成本中排名第三,其通过大规模生产有望进一步降低成本。基于此,研究人员将重点转向简化外部树脂结构的设计,该结构虽对成本影响相对较小,但简化设计能够提升功率密度。
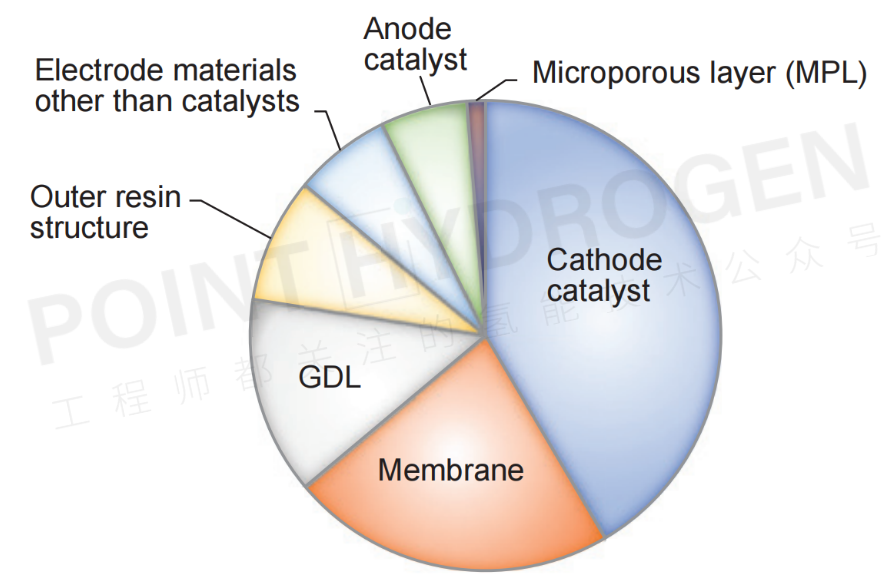
为了提升原有燃料电池堆的性能和耐久性,采取了以下措施:(1)减少电极催化剂中的铂(Pt)用量;(2)减少电解质膜中离子体的用量;(3)优化外部树脂结构的设计。
然而,由于MEA的耐久性与铂和离子体的用量成反比关系,因此在降低成本的同时维持高耐久性成为一大挑战。为此,研究人员为每个UEA组件开发了退化模型,用于定量分析材料退化对耐久性的影响。基于这些模型,针对不同材料的特性,通过控制操作环境,确保燃料电池堆在成本降低的同时保持可靠的耐久性。新结构堆中UEA的结构如图3所示。发电单元由单个UEA夹在两个双极板(BPPs)之间构成。
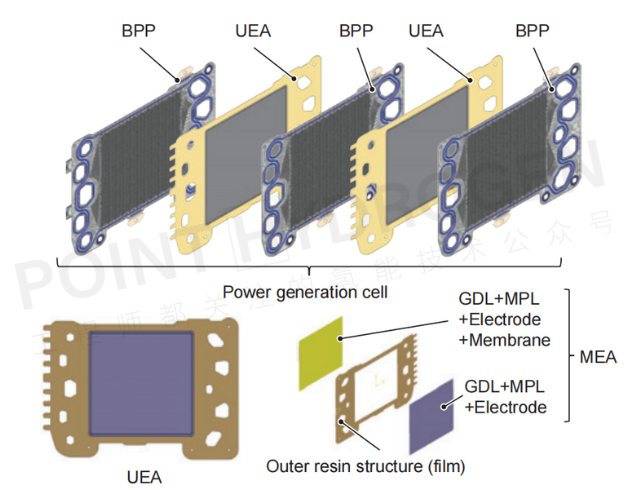
02 简化外部树脂结构
2.1 树脂膜
为简化外部树脂结构设计,将流道结构集成到双极板中,从而不再需要在UEA树脂框架中设置流道。在该UEA中,外部结构通过采用冲压成型的通用树脂膜得以简化。通过采用膜的形式,将线性膨胀系数接近于双极板材料SUS的通用树脂膜进行层压,形成如图3所示的UEA结构。
之前采用精密注塑成型工艺,需要使用昂贵的工程塑料,且由于成型特性,注塑成型厚度需达到250微米或以上;而使用通用树脂膜后,该厚度减少了50%以上,从而提升了体积功率密度。此外,与上一代电堆相比,这一设计使单件成本减少了一半。
2.2 强度耐久度
如图3所示,树脂膜被夹在双极板之间。在发电过程中,阴极和阳极气体在双极板流道中流动时产生的气体压力差可能会对树脂膜施加应力。通过设定双极板之间的树脂膜保留间隔距离(retention interval distance),有效地缓解了该应力。
此外,由于发电过程中产生的水分会导致水解作用(hydrolysis),从而引发化学降解,因此设计时考虑了树脂膜在化学降解后强度降低的情况,并结合阴极与阳极之间的气体压力差要求,优化了机械强度设计。通过有限元方法对气体压力差进行了模拟。图4显示了模拟结果,确认了应力与双极板间保留间隔距离之间的关系。通过控制双极板之间的间隔距离,成功抑制了应力,实现了足够的强度耐久性。
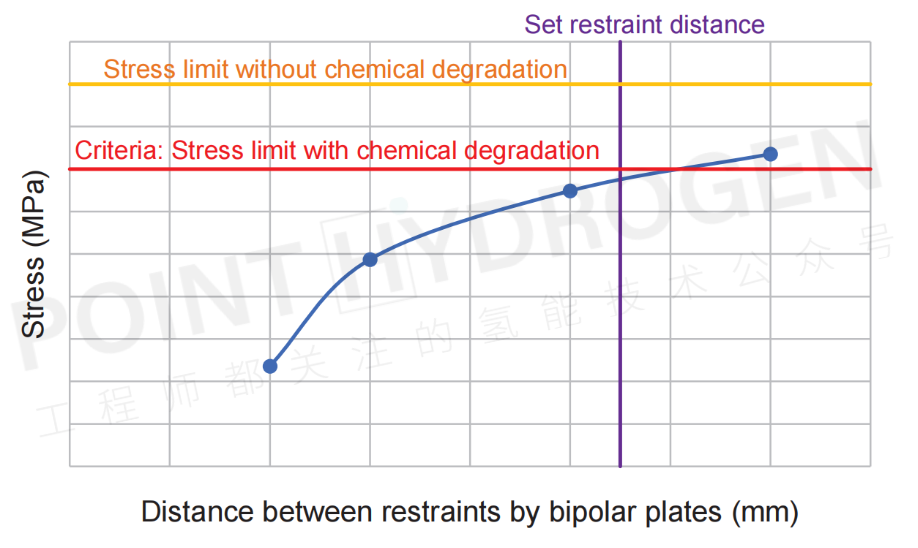
03 结论
与通用汽车公司合作开发的新型低成本UEA已成功应用于新结构的燃料电池堆,取得了显著成果:其耐久性提升至原来的两倍多,成本降至原燃料电池堆的1/3,同时保持了与以往相同的输出性能。
具体来说,通过采用铂合金催化剂、多孔碳以及低支撑率等设计,这些改进可有效抑制退化,使电极中的铂用量减少至原UEA的1/5。通过解决化学和机械降解问题,结合专有的涂层工艺,将电解质膜厚度减至原燃料电池堆的3/5。此外,外部树脂结构的设计也得到了简化,使得使用厚度减半的树脂膜成为可能。