燃料电池被视为一种循环型清洁能源装置,不排放二氧化碳或有害物质,能够有效应对全球变暖和能源危机。本田自20世纪80年代起便致力于燃料电池技术的实用化研究。本文将探讨双极板(Bipolar Plate, BPP),该组件是新型结构燃料电池堆中多层电池的重要组成部分之一。该多层电池采用单体化电极组件(Unitized Electrode Assembly, UEA),并结合两个BPP与冷却剂流通,构成如图1所示的电池结构。
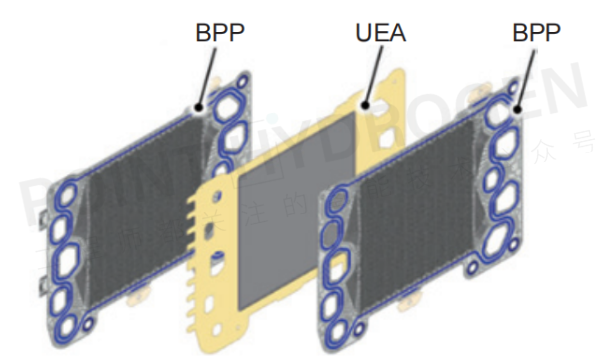
图2展示了对双极板BPP的功能要求:
-
向单体化电极组件UEA供应氢气和氧气;
-
流通冷却剂以冷却BPP和UEA;
-
对氢气、氧气和冷却剂进行密封;
-
在电池之间提供导电性;
-
在发电环境中提供耐腐蚀性能。
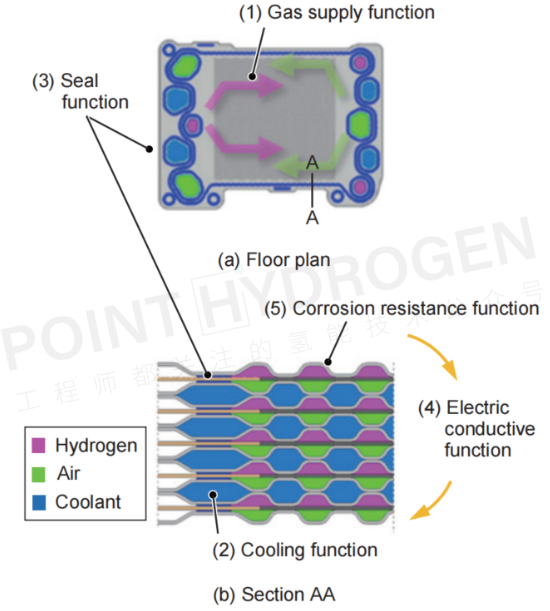
01 新型GLC涂层
在传统双极板(BPP)设计中,不锈钢表面通常采用海岛结构(sea-island)镀金处理,并在暴露的不锈钢区域形成钝化膜,从而兼顾导电性与耐腐蚀性能的需求。
双极板(BPP)通常以不锈钢作为基材,但在高温高湿的酸性腐蚀环境中,暴露的不锈钢区域的钝化膜可能会受到破坏,从而导致铁离子溶出,这会降低离子交换膜的耐久性。因此,亟需提升以不锈钢为基材的双极板的耐腐蚀性能。
新开发的双极板(BPP)通过在不锈钢基材上涂覆GLC(graphite-like carbon)层和中间钛(Ti)层,不仅提高了耐腐蚀性,还有效抑制了不锈钢基材的暴露,同时保持了良好的导电性。与传统的镀金处理相比,这种方法具有更低的成本,如图3所示。
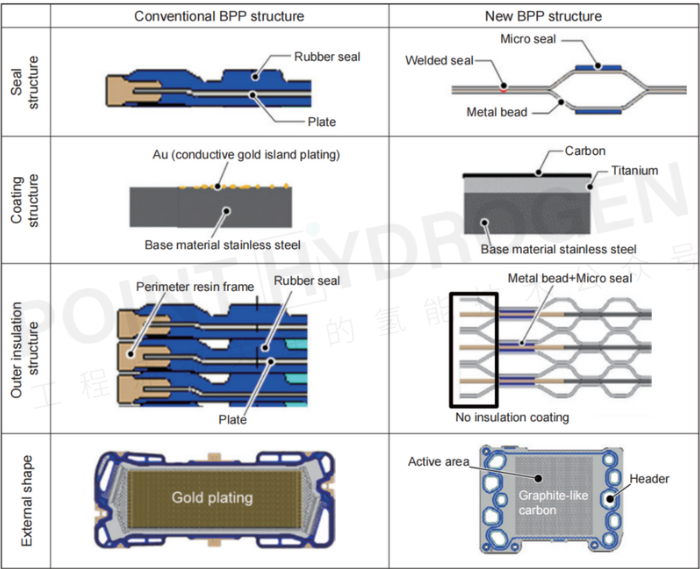
此外,GLC层和中间Ti层可以在不锈钢基材上连续涂覆,无需在冲压后进行批量涂覆加工,从而提高了生产效率。GLC层和中间Ti层提供了可靠的耐腐蚀性能,即使在高温高湿的酸性腐蚀环境中,采用GLC和Ti层涂覆后,铁离子的溶出量也降低至不锈钢的约1/30。
相比之下,如果在表面处理后进行冲压,基材在冲压过程中会发生拉伸,导致GLC层和中间Ti层产生裂纹,并因与模具摩擦而出现划痕,从而导致不锈钢基材暴露,如图4所示。
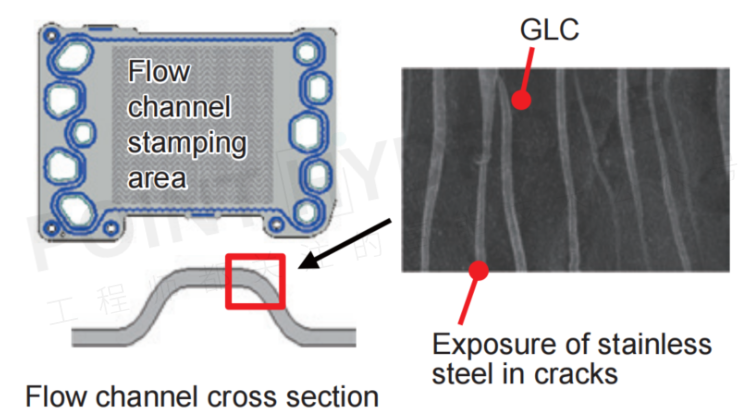
已知双极板(BPP)的铁离子溶出量与不锈钢基材的暴露程度密切相关。因此,在设计流道的横截面形状时,需要考虑基材在冲压过程中的拉伸情况,以抑制不锈钢基材的暴露程度。通过降低冲压后不锈钢的暴露率,新开发的双极板将铁离子溶出量降低至传统双极板的1/10,如图5所示,同时也有效降低了涂覆工艺的成本。
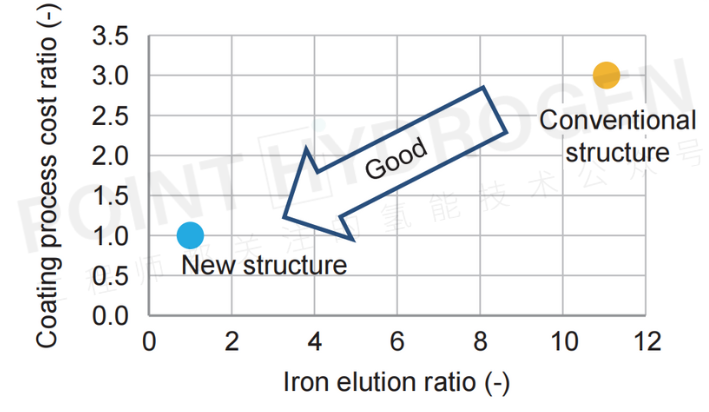
02 消除树脂成型与绝缘检测工序
传统双极板(BPP)通过周边橡胶涂层提供绝缘性能,而新结构则依据IEC60664-1的要求,为电池(发电部件)设定了爬电距离和间隙距离,如图6所示。此外,采用无周边橡胶涂层的结构,省去了绝缘检测工序。与旧型号相比,这种设计使每片电池的橡胶用量减少了6%,树脂用量减少了54%。同时,还消除了树脂成型和绝缘检测工序。
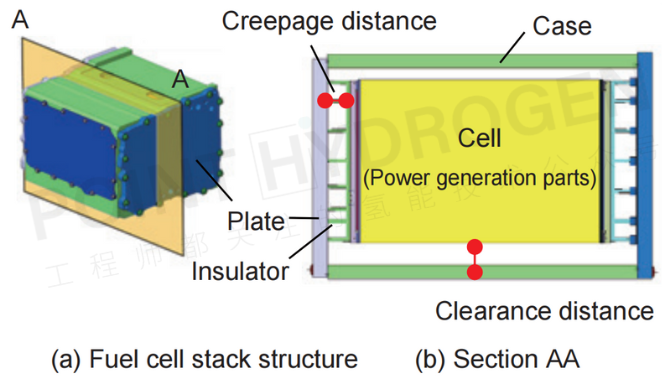
03 生产工艺设计
图7展示了传统结构与新结构的生产工艺流程。在传统工艺中,表面处理是在冲压后作为独立工序进行的,而新结构则采用GLC涂覆卷材直接进行冲压,这不仅缩短了工艺时间,还提高了循环效率。
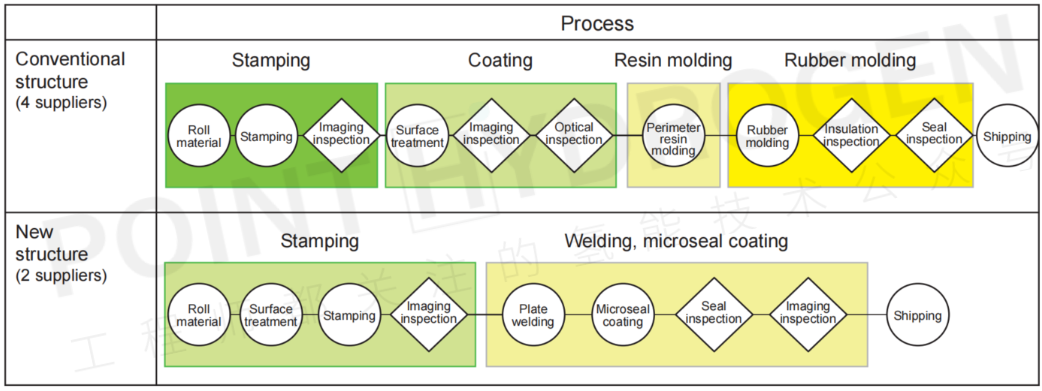
图8展示了金属密封珠(MBS)和流道区域冲压工序的详细内容。新结构采用了上述的双击冲压工艺(2Hit),并实现了激光刻印和检测工序的全自动化,以满足质量控制要求。通过全面自动化树脂成型、绝缘检测、激光刻印和检测工序,新型双极板结构将生产周期缩短至传统结构的1/20。
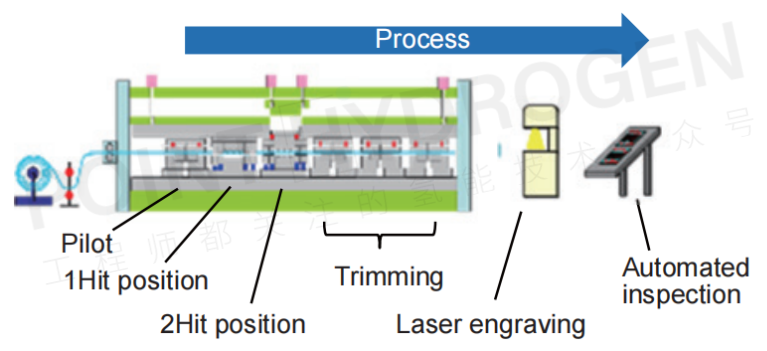
04 结论
通过提升生产效率并优化材料和功能,开发出了一种新型双极板(BPP)结构,该结构在实现密封功能、耐腐蚀性能和成本降低方面取得了以下成果:
密封功能优化
金属密封珠部件的设计采用了具有均匀面内压缩载荷特性的横截面形状和平面布局,并引入了承载结构,以提升碰撞情况下的密封性能。通过使用金属密封珠和微密封结构,设计有效减少了线压下降,同时保持了良好的密封功能。对焊接密封部件的焊接条件进行了优化,有效防止了BPP翘曲和敏化,同时确保了足够的结合强度。
冲压成形优化
采用双击模具(2Hit)结构,有效抑制冲压过程中的回弹,减少了流道翘曲问题。金属密封珠部件也采用了双击模具结构,并加入了加工硬化,从而提升了金属密封珠的压缩载荷性能。
耐腐蚀性能提升
通过在卷材上应用GLC涂层,并采用考虑流道形状、抑制冲压过程中不锈钢暴露程度的设计,将铁离子溶出量降低至传统结构的1/10。
工艺效率改进
新结构采用GLC涂覆卷材进行冲压,缩短了工艺时间并提升了循环效率。基于IEC60664-1标准,为电池(发电部件)设置了爬电距离和间隙距离,同时采用了无周边橡胶涂层的结构。